How Does the Manufacturer Ensure Quality Control for Deep Heat Patches OEM?
Quality control is essential in the production of Deep Heat Patches OEM products, as it ensures that each patch is safe, effective, and consistent. For companies seeking to develop Private Label Deep Heat Patches or customize products, selecting a reliable Deep Heat Patches Manufacturer with stringent quality control measures is crucial. This article explores the steps manufacturers take to ensure quality in the OEM process, from ingredient selection to packaging and distribution. With a deep dive into industry standards, we’ll examine why these quality practices are necessary for brands aiming to offer top-tier Custom Deep Heat Patches and how working with a dependable Deep Heat Patches Supplier can support this goal.
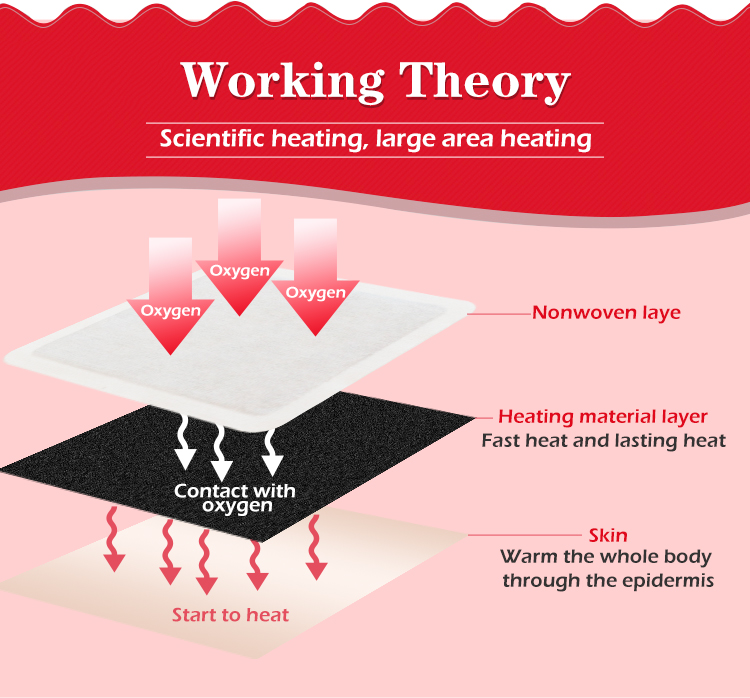
1. Ingredient Selection and Sourcing
The quality control process begins with the selection of ingredients. High-quality materials are critical in delivering consistent therapeutic effects, safety, and customer satisfaction.
- Trusted Ingredient Sources: Reputable Deep Heat Patches Manufacturers source raw materials from certified suppliers who adhere to strict industry standards. This ensures that every ingredient meets specifications for purity, potency, and consistency.
- Testing for Purity and Potency: Before any ingredient is used, it undergoes rigorous testing. These tests check for potential contaminants like heavy metals, pesticides, and microbes, ensuring that the materials are safe and pure.
Through careful sourcing and testing, Deep Heat Patches OEM providers can guarantee that only the finest ingredients are used in their products, which is vital for maintaining consistent quality across batches.
2. Manufacturing Process Controls
Manufacturers of Deep Heat Patches follow strict guidelines to ensure that every patch is produced to meet high standards. This process includes everything from formulation to production, all of which is monitored to prevent variations.
- Standardized Formulation Procedures: Formulation is key to the effectiveness of Deep Heat Patches. Manufacturers adhere to standardized procedures to ensure consistency in the ratio of active ingredients, resulting in uniform heating effects and safety across batches.
- Adherence to Good Manufacturing Practices (GMP): Most Deep Heat Patches Manufacturers follow GMP, which outlines strict protocols for cleanliness, personnel training, equipment maintenance, and more. GMP-certified facilities provide assurance that every stage of production meets international quality standards.
These controls enable manufacturers to produce Custom Deep Heat Patches with the reliability and safety necessary for therapeutic use, which is critical for building consumer trust in Private Label products.
3. Quality Assurance Testing
In addition to ingredient testing, manufacturers conduct comprehensive quality assurance testing on finished patches. This phase ensures that each patch delivers the intended heating effect, adheres correctly, and is free from defects.
- Consistency and Stability Testing: Manufacturers evaluate patches for consistent heat output, adhesion, and stability over time. Stability tests simulate real-life conditions, such as storage and transport, to ensure the product remains effective and safe throughout its shelf life.
- Skin Compatibility Testing: Given that patches are applied directly to the skin, manufacturers conduct skin irritation tests to verify that the patches are safe for all skin types. This testing reduces the risk of adverse reactions and ensures that Private Label Deep Heat Patches meet customer expectations for comfort and safety.
By thoroughly testing each batch, Deep Heat Patches OEM providers confirm that the product meets both regulatory standards and customer expectations for performance.
4. Packaging and Labeling Standards
Packaging is another critical aspect of quality control, as it impacts both product safety and brand perception. Proper packaging ensures that Deep Heat Patches remain effective until used.
- Protective Packaging Materials: Manufacturers select packaging materials that protect patches from moisture, heat, and contamination. Sealed packaging also helps maintain product integrity, extending the shelf life of the patches.
- Clear, Compliant Labeling: Labels provide essential information such as ingredients, usage instructions, warnings, and expiry dates. A reputable Deep Heat Patches Supplier will ensure that labeling complies with regulatory requirements, helping brands maintain transparency and customer trust.
Effective packaging and labeling reinforce product quality and reassure customers, making them more likely to trust and repurchase Custom Deep Heat Patches.
5. Regulatory Compliance and Certification
Compliance with industry regulations and standards is a significant aspect of quality control for Deep Heat Patches. Reputable manufacturers ensure that their facilities and processes meet legal requirements in every market they serve.
- ISO and Other Certifications: Many Deep Heat Patches Manufacturers obtain ISO certification to demonstrate adherence to global standards for quality management. Certifications add credibility to the brand and indicate that the manufacturer maintains high standards in product quality.
- FDA Compliance: For manufacturers supplying to the U.S., FDA compliance is essential. FDA-certified manufacturers follow stringent protocols, ensuring that their products are safe, accurately labeled, and meet all health requirements. This is especially important for brands developing Private Label Deep Heat Patches intended for U.S. distribution.
Manufacturers committed to regulatory compliance offer additional peace of mind to brands, enabling them to confidently promote their products as safe and reliable.
6. Quality Control for Customized Deep Heat Patches
For businesses interested in OEM services to create unique products, quality control extends beyond standard procedures to accommodate customization. Customized patches require tailored testing to ensure consistency with the brand’s specifications.
- Custom Ingredient Ratios: When developing Custom Deep Heat Patches, manufacturers adjust ingredient ratios to create desired heat levels and therapeutic effects. This involves additional testing to confirm the product aligns with the brand’s specifications.
- Customized Design Testing: Brands may require different patch shapes, sizes, or adhesive strengths. Manufacturers conduct tests on these customized elements to verify effectiveness and ensure the patches remain comfortable and functional for end-users.
Through extensive testing and attention to detail, OEM manufacturers can deliver tailored solutions that maintain the same high standards as standard products, enabling brands to confidently offer unique, high-quality options.
7. Continuous Improvement and Feedback Integration
Quality control is an ongoing process that doesn’t stop once the product is manufactured. Leading Deep Heat Patches Suppliers continuously seek ways to improve their products, incorporating feedback from clients and end-users.
- Customer Feedback and Quality Audits: Manufacturers regularly review customer feedback to identify any potential areas for improvement. Quality audits further assess the effectiveness of quality control measures, helping manufacturers enhance their processes.
- Product Innovation: Manufacturers focused on continuous improvement invest in research and development. By staying at the forefront of innovation, these manufacturers can introduce new technologies, such as enhanced adhesion or heat modulation, that improve user experience.
Commitment to continuous improvement enables Deep Heat Patches OEM providers to stay competitive and maintain high quality standards, benefiting both brands and end-users.
Conclusion
Ensuring quality control for Deep Heat Patches OEM involves a multifaceted approach that includes rigorous testing, regulatory compliance, careful sourcing, and adherence to manufacturing standards. By working with a reputable Deep Heat Patches Manufacturer and Deep Heat Patches Supplier that prioritizes quality, brands can confidently provide effective, safe, and reliable heat patches to their customers. Whether businesses are looking to create Private Label Deep Heat Patches or customize patches to meet unique needs, choosing a manufacturer with strong quality control measures guarantees a product that meets the highest standards.
Related Questions
Q1: What should I look for when choosing a Deep Heat Patches Manufacturer?
A1: Look for manufacturers with certifications like GMP or ISO, strong quality control protocols, and experience in producing high-quality patches.
Q2: How can a Deep Heat Patches Supplier help with product customization?
A2: Suppliers with OEM capabilities can customize ingredients, heat levels, and patch sizes to meet specific brand requirements, enhancing the customer experience.
Q3: Are Private Label Deep Heat Patches safe to use?
A3: Yes, if produced by a reputable manufacturer with rigorous quality testing, Private Label Deep Heat Patches are designed to be safe and effective for end-users.
Q4: What role does regulatory compliance play in the quality of Deep Heat Patches?
A4: Regulatory compliance ensures that patches meet safety and efficacy standards, protecting users and establishing credibility for the brand.
Q5: Can Custom Deep Heat Patches provide different heat levels?
A5: Yes, OEM manufacturers can adjust heat intensity to offer customized products that meet specific therapeutic needs.
Working with a quality-driven Deep Heat Patches Manufacturer enables businesses to provide trusted, effective products to customers, which is essential for building a reputable brand in the health and wellness market.